CURRENT TECHNOLOGY AND ITS LIMITATIONS
The current tilt-rotor design features two turbine engines mounted behind prop-rotors at the wingtips. OEI performance and safety requires the two power-plants be mechanically coupled through a complicated network of transmissions, clutches, gear-boxes, drive-shafts, and back-up systems. These systems alone account for over 25% of the empty weight of the current design and an even greater percentage cost of manufacturing and service. This substantial weight is only overcome through the deployment of larger capacity turbines and rotors resulting in additional increases in weight, and again increased component costs and higher fuel consumption. The resultant loss of efficiency decreases speed, payload and range as well as limits the mission, and inflates the cost of procurement and operation. The current design is further plagued by the position of the power-plants. The design suffers from complicated CG (center of gravity) restrictions stemming from the position of significant weight at the farthest stations from the CG. This not only frustrates the performance throughout the flight envelop, especially role, but again adds significant weight for materials needed to strengthen the wings and the extensive utilization of electronic stabilization systems mandatory for all flight regimes.
PATENTED NEW TECHNOLOGY OVERCOMES ALL LIMITATIONS
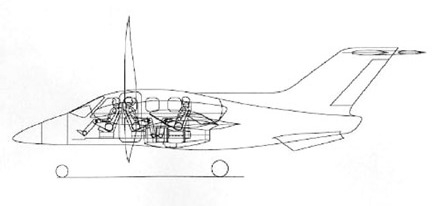
AAT’s concept incorporates tip-jet driven prop-rotors that do not require the aforementioned heavy transmissions, gearboxes, driveshafts and a tremendous number of required support, stabilization and ancillary components. Thus all mechanical linkage between turbines is removed along with its corresponding mass and costly TBO’s. The compressed exhaust gas from the fan-jet engines is ducted to a manifold (see schematic representation) having valves that control power to the prop-rotors and to the jet exhaust nozzles as supplemental thrust for forward propulsion and yaw control. Thrust in forward flight is thus obtained from any combination of thrust from the tip-jet driven prop-rotors and jet exhaust directly from the engines.
In level flight, proprietary flight computers determine the most efficient use of the jet exhaust stream, as it balances the amount of jet thrust out the rear to the amount used to drive the prop-rotors. This method also allows for adjusting for quietest operation as determined by the mission at hand. Other functions of the computers are to capture, measure and analyze environmental, mission, and flight data to constantly regulate the production and flow of exhaust gases for VTOL operations, and to achieve the most efficient and/or quietest operation.
A very important feature is to provide multiple power-plant safety while keeping the mass near the fuselage, under the wings and close to the Center of Gravity. Engines can be placed in any convenient place, and air ducts provide the coupling to the prop-rotors. Safety is dramatically increased in the event of a critical OEI emergency because the manifold and associated valving will instantly balance the compressed exhaust gases to the prop-rotors, exhaust nozzles and/or reaction jets for additional stabilization and attitude control. This design completely eliminates dead or critical engine scenarios.
With this technology, the aircraft is more efficient, faster, immensely lighter, drastically less complex and radically less expensive to purchase and maintain than its shaft-driven counterpart.
ESTIMATED 25 PERCENT IMPROVEMENT IN COSTS & PERFORMANCE
The commercial concept, pictured in the patent document, is an eight-place, 7,650-pound vehicle, powered by two Williams FJ-33, 800 pound thrust turbofan jet engines. The prop-rotors are 19 feet in diameter. Preliminary engineering indicates this craft will cruise at 335 knots at sea level and nearly 400 knots at FL250.
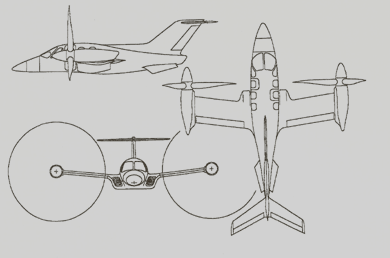
If we compare typical 6 to 9 passenger turbo-prop aircraft to today’s tilt-rotors of the same class, we would find very large differences in cost, operating cost, weight, weight fraction, and performance. Yet, with our technology, it is possible for tilt-rotors to be on the same playing field as other turbo-props such as the King Air, the Cheyenne, and the Embraer Xingu in terms of all of the previously mentioned factors. This is extremely significant, and will definitely put the tilt-rotor firmly on solid ground as an aircraft that will see phenomenal growth during the next ten to twenty years.
Another important fact about our tip-jet powered prop-rotors is they can be more efficient than shaft driven counterparts due to several factors including thrust augmentation, which we have estimated at 11.8 for the aircraft pictured herein. This means that for every pound of thrust used by the tip-jets, the prop-rotors will produce 11.8 pounds of lift or thrust. Yes, this is very significant!
FURTHER INFORMATION
You may register at this Website, or talk with our president for further information. Contact information is on the Communication page.